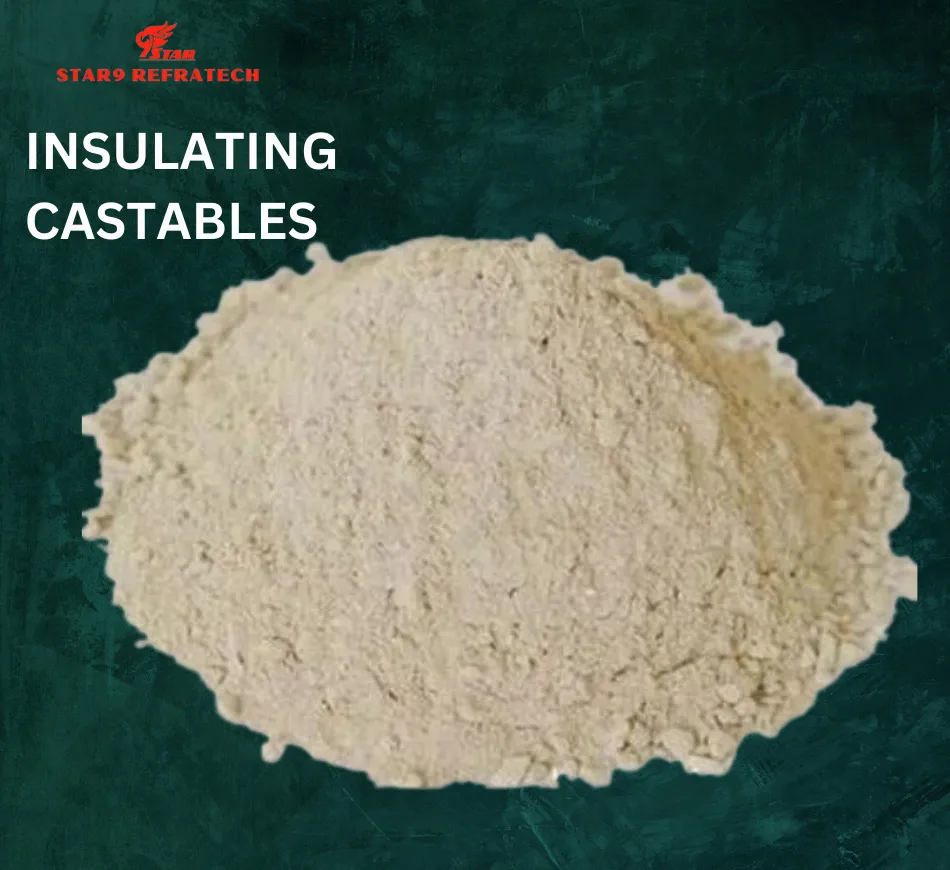
Insulating Product Femily
Brand Name: – | SR INSULCAST 4 | SR INSULCAST 7 | SR INSULCAST 9 | SR INSULCAST 11 | SR INSULCAST 13 | SR INSULCAST 15 | SR POURABLE INSULATION | SR INSULCAST 11 Li | SR INSULCAST 11 Liz | |||
Type | Low Density Insulating Castable | Low Density Insulating Castable | Medium density insulating Castable | Medium density insulating Castable | Moderate density insulating Castable | Moderate density insulating Castable | Insulating Castable Used By Pouring | Medium density insulating Castable | Medium density insulating Castable | |||
Nature of Bond | Hydraulic | Hydraulic | Hydraulic | Hydraulic | Hydraulic | Hydraulic | Hydraulic | Hydraulic | Hydraulic | |||
Installation | Tamping | Tamping | Tamping | Tamping | Tamping | Tamping | Pouring | Tamping | Tamping | |||
Raw Material Base | Exfoliated Vermiculite | Exfoliated Vermiculite | Insulating Aggregate | Insulating Aggregate | Insulating Aggregate | Insulating Aggregate | Exfoliated Vermiculite | Insulating Aggregate | Insulating Aggregate | |||
Max Service Temp. | 1000 0C | 1100 0C | 1200°C | 1300°C | 1350°C | 1350°C | 900°C | 1350°C | 1300°C | |||
Max Grain Size | 6 mm | 6 mm | 6 mm | 6 mm | 6 mm | 6 mm | 6 mm | 6 mm | 6 mm | |||
Water Required for Casting | 70-100 % | 40-70 % | 35-40% | 25-35% | 25-30% | 23-28% | 55-70% | 30-35% | 40-45% | |||
Chemical Analyses: – (%) | ||||||||||||
Al2O3 : | — | — | – | – | – | — | — | – | — | |||
Fe2O3 : | 11.0 Max | 8.5 Max | 6.00 Max | 3.50 Max | 3.50 Max | 3.20 Max | 9.0 Max | 1.50 Max | 1.20 Max | |||
CaO : | — | — | – | – | – | — | — | – | — | |||
Physical Properties: – | ||||||||||||
B. D (gm/cc)
Drying at 110°C/24 hrs. |
0.55 Max | 0.85 Max | 1.00 Max | 1.25 Max | 1.45 Max | 1.60 Max | 0.70 Max | 1.25 Max | 1.00 Max | |||
Cold Crushing Strength (Kg/cm2): | ||||||||||||
Drying at 110°C/24 hrs. | 4 Min | 12 Min | 15 Min | 35 Min | 50 Min | 90 Min | 15 Min | 45 Min | 15 Min | |||
Fired at 800°C/3hrs. | 2 Min | 4 Min | 6 Min | 25 Min | 30 Min | 60 Min | 12 Min | 30 Min | 10 Min | |||
Fired at 1100°C/3hrs. | — | 6 Min | — | 25 Min | 30 Min | 60 Min | — | 30 Min | 8 Min | |||
Fired at 1200°C/3hrs. | — | — | 10 Min | — | — | — | — | — | — | |||
Fired at 1300°C/3hrs. | — | — | — | 40 Min | 50 Min | 70 Min | — | 50 Min | 15 Min | |||
Thermal Properties: – | ||||||||||||
Permanent Linear Change (%) | ||||||||||||
Fired at 800°C/3hrs. | ± 0.40 Max | ± 0.80 Max | ± 0.60 Max | ± 0.20 Max | ± 0.20 Max | — | ± 1.50 Max | — | — | |||
Fired at 1000°C/3hrs. | ± 0.60 Max | ± 1.20 Max | — | — | — | — | — | — | — | |||
Fired at 1100°C/3hrs. | — | — | ± 1.00 Max | ± 1.00 Max | ± 0.80 Max | ± 0.20 Max | — | ± 0.20 Max | ± 0.20 Max | |||
Fired at 1300°C/3hrs. | — | — | — | — | — | ± 1.00 Max | — | ± 1.00 Max | ± 1.00 Max | |||
Thermal Conductivity , K Cal/m/hr/0C | ||||||||||||
@500 0C | 0.10 Max | 0.18 Max | 0.28 Max | 0.31 Max | 0.33Max | 0.44Max | 0.20 Max | 0.21 | 0.22Max | |||
Water requirements indicated are based on laboratory test conditions. Actual water requirement may vary subject to site conditions. The properties shown are for vibratory cast material only unless specified otherwise. All values are based on test results on standard bars of size 160x40x40 mm. Test methods are guided by and based on various Indian Standards (IS). | ||||||||||||
Brand Name: – | SR INSULCAST 13 Li | SR INSULCAST 15 Li | SR INSULCAST 8 S | SR INSULCAST 10 S | SR CAST 97 L | SR INSULCAST 9 HS | ||
Type | Moderate density insulating Castable | Moderate density insulating Castable | Low density insulating Castable | Medium density insulating Castable | Insulating Castable For 18000 C Temp. | Medium density insulating Castable (High Strength) | ||
Nature of Bond | Hydraulic | Hydraulic | Hydraulic | Hydraulic | Hydraulic | Hydraulic | ||
Installation | Tamping | Tamping | Tamping | Tamping | Tamping | Tamping | ||
Raw Material Base | Insulating Aggregate | Insulating Aggregate | Insulating Aggregate | Insulating Aggregate | Bubble Alumina | Insulating Aggregate | ||
Max Service Temp. | 1400°C | 1400°C | 1300°C | 1100°C | 1800°C | 1200°C | ||
Max Grain Size | 6 mm | 6 mm | 6 mm | 6 mm | 6 mm | 6 mm | ||
Water Required for Casting | 25-30% | 23-28% | 46-50% | 40-46% | 13-18 % | 35-40% | ||
Chemical Analyses: – (%) | ||||||||
Al2O3 : | – | — | 40 Min | – | 94.0 Min | 40.0 Min | ||
Fe2O3 : | 1.50 Max | 1.50 Max | 1.0 Max | 6.0 Max | 0.3 Max | 3.0 Max | ||
CaO : | – | — | – | – | 5.0 Max | 8.0 Max | ||
Physical Properties: – | ||||||||
B. D (gm/cc)
Drying at 110°C/24 hrs. |
1.45 Max | 1.60 Max | 0.900 Max | 1.10 Max | 1.65Max | 1.00 Max | ||
Cold Crushing Strength (Kg/cm2): | ||||||||
Drying at 110°C/24 hrs. | 80 Min | 130 Min | 25 Min | 20 Min | 70 Min | 20 Min | ||
Fired at 800°C/3hrs. | 40 Min | 75 Min | 20 Min | 15 Min | 60 Min | 8 Min | ||
Fired at 1100°C/3hrs. | 40 Min | 75 Min | — | — | 40 Min | — | ||
Fired at 1200°C/3hrs. | — | — | — | 12 Min | — | 15 Min | ||
Fired at 1350°C/3hrs. | — | 90 Min | 30 Min | — | — | — | ||
Fired at 1550°C/3hrs. | 50 Min | — | — | — | 60 Min | — | ||
Thermal Properties: – | ||||||||
Permanent Linear Change (%) | ||||||||
Fired at 800°C/3hrs. | — | — | ± 0.30 Max | ± 0.80 Max | ± 0.20 Max | ± 0.60 Max | ||
Fired at 1100°C/3hrs. | ± 0.20 Max | ± 0.20 Max | ± 0.50 Max | ± 1.20 Max | ± 0.20 Max | ± 1.00 Max | ||
Fired at 1350°C/3hrs. | — | ± 1.00 Max | — | — | — | — | ||
Fired at 1550°C/3hrs. | ± 0.80 Max | — | — | — | ± 1.00 Max | — | ||
Thermal Conductivity , K Cal/m/hr/0C | ||||||||
@500 0C | 0.40Max | 0.44Max | 0.22 Max | 0.22 Max | 1.10 Max | 0.28 Max | ||
Water requirements indicated are based on laboratory test conditions. Actual water requirements may vary subject to site conditions. The properties shown are for vibratory cast material only unless specified otherwise. All values are based on test results on standard bars of size 160x40x40 mm. Test methods are guided by and based on various Indian Standards (IS). |
Brand Name: – | SR INSULCAST 22 Li
( AS PER MIDREX Specification) |
SR INSULCAST 11 Liz
( AS PER MIDREX Specification) |
SR LCC 60 A
( AS PER MIDREX Specification) |
SR GUN 55
( AS PER MIDREX Specification) |
||||
Type | Medium density Insulating Castable | Light Weight Insulating Castable(Low Iron) | Casting Type Abrasion Resistance Castable (Low Iron) | Gunning Type Abrasion Resistance Castable (Low Iron) | ||||
Nature of Bond | Hydraulic | Hydraulic | Hydraulic | Hydraulic | ||||
Installation | Tamping | Tamping | Vibration Casting | Gunning | ||||
Raw Material Base | Insulating Aggregate & Perlite | Insulating Aggregate & Perlite | Andalusite | Calcined Clay | ||||
Max Service Temp. | 1093°C | 1260°C | 1480 0C | 1480 0C | ||||
Max Grain Size | 6 mm | 0 – 6 mm | 0-6 mm | 0-6 mm | ||||
Water Required for Casting | 40-50% | 55-65 % | 6-8 % | At Nozzle | ||||
Chemical Analyses: – (%) | Typical | Specification | Typical | Specification | Typical | Specification | Typical | Specification |
Al2O3 : | 49.6 | 45 to 50 | 42.50 | 40-43 | 50.50 | 45-53 | 48.50 | 45-53 |
Fe2O3 : | 0.90 | 0.5 to 1.3 | 1.20 | 0.9-1.3 | 0.90 | 0.8-1.3 | 1.00 | 0.8-1.3 |
SiO2 : | 32.0 | 30 to 40 | 35.30 | 35-37 | 40.0 | 34-48 | 42.0 | 35-48 |
Physical Properties: – | ||||||||
B. D (gm/cc)
Drying at 105°C/24 hrs. |
1.10 | 0.96 to 1.12 | 0.88 | 0.83-0.93 | 2.20 | 2.05 -2.24 | 2.08 | 2.05 -2.24 |
Cold Crushing Strength (Kg/cm2): | ||||||||
Drying at 105°C/24 hrs. | 97 | 80-100 | 35 | 30-37 | 600 | 350-632 | 355 | 350-632 |
Fired at 538°C/3hrs. | 65 | 60-70 | 30 | 29-32 | 500 | 280-562 | 285 | 280-562 |
Fired at 815°C/3hrs | 64 | 60-63 | 30 | 28-35 | 600 | 350-632 | 355 | 350-632 |
Fired at 1093°C/3hrs | 55 | 53-56 | —- | —- | 540 | 315-580 | 325 | 315-580 |
Fired at 1205°C/3hrs | — | — | 35 | 28-35 | ||||
Thermal Properties: – | ||||||||
Refractoriness, Orton / 0 C | +14 | Service Temp. 10930C | +14 | Service Temp. 12600C | +32 | Service Temp
1315 to 1480 0C |
+32 | Service Temp
1315 to 1480 0C |
PLC (%) | ||||||||
Fired at 815°C/3hrs. | -0.10 | -0.9 Max | -0.30 | – 0.5 to -0.7 | -0.03 | +0.1to -0.7 | -0.15 | +0.1to -0.7 |
Fired at 1093°C/3hrs. | -0.53 | -1.10 Max | — | — | -0.80 | -0.4 to -1.20 | -1.00 | -0.4 to -1.20 |
Fired at 1205°C/3hrs | —- | —- | – 1.0 | -1.7 to –1.9 | — | — | — | — |
Thermal Conductivity , K Cal/m/hr/0C | ||||||||
@260 0C | — | — | 0.10 | 0.161 – 0.164 | — | — | — | — |
@538 0C | 0.24 | 0.24-0.25 | 0.13 | 0.174-0.177 | 0.840 | 0.818- 0.843 | 0.820 | 0.818- 0.843 |
@815 0C | 0.28 | 0.27-0.30 | 0.17 | 0.198-0.205 | 0.890 | 0.868 – 0.893 | 0.870 | 0.868 – 0.893 |
Water requirements indicated are based on laboratory test conditions. Actual water requirements may vary subject to site conditions. The properties shown are for vibratory cast material only unless specified otherwise. All values are based on test results on standard bars of size 160x40x40 mm. Test methods are guided by and based on various Indian Standards (IS). |